Bridge repair
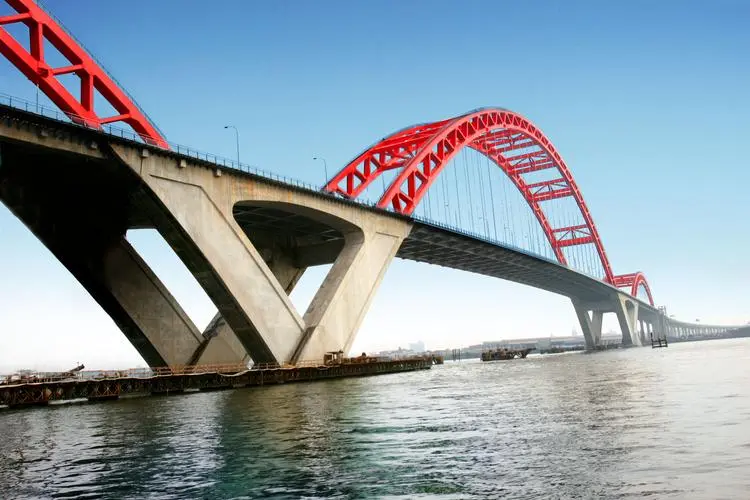
How to Use microfine Cement to Repair the Bridge
Bridges are vital infrastructures that connect people and places, but they are also exposed to various environmental and operational stresses that can cause damage and deterioration over time. To ensure the safety and functionality of bridges, it is essential to repair and maintain them regularly using appropriate materials and methods.
One of the materials that can be used for bridge repair is microfine cement, which is a Portland cement based grouting material composed of microfine particles with a specific surface area of over 800 m2/kg . microfine cement is designed for injection into and penetration of tight joints, fissures and pore spaces in rock and soil, which are common in bridge foundations and abutments. microfine cement has several advantages over ordinary Portland cement, such as better penetration, water tightness, durability and sulphate resistance.
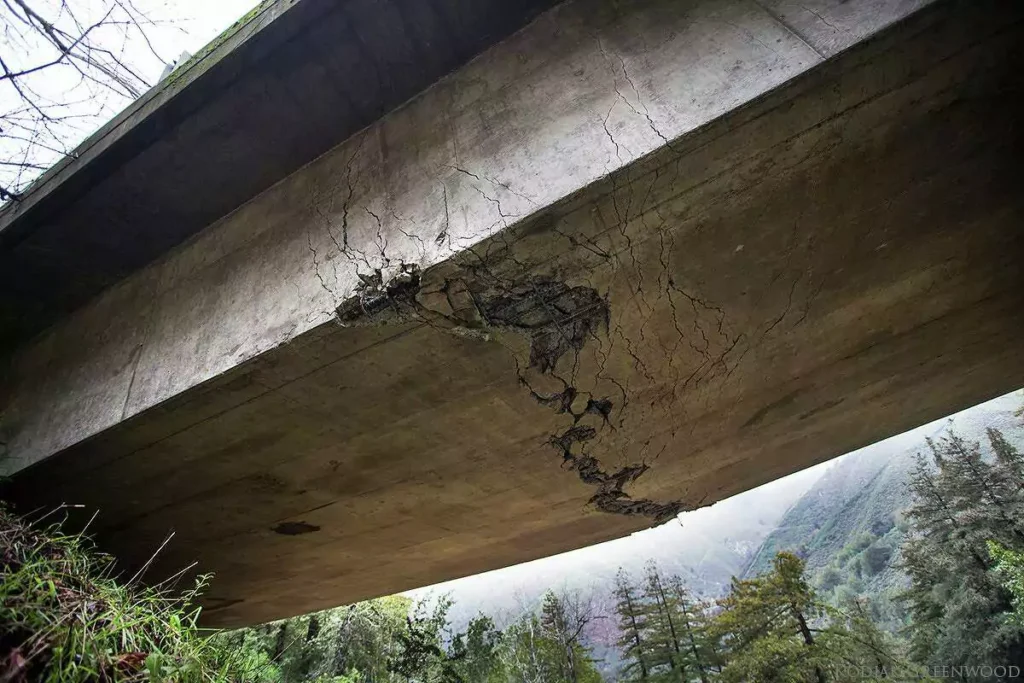
The materials used for the grouting project include the microfine cement, admixtures, water and equipment. The type and properties of microfine cement depend on the application and site conditions, but generally it should have a high fineness, low alkali content, controlled setting time and good compatibility with admixtures . Some examples of microfine cement products are HSR1000, HSR1340, MFPC1000, MFPC1250, MFPC2000. Admixtures are added to the microfine cement to modify its properties, such as accelerating or retarding the setting time, reducing the water-cement ratio, improving the flowability or increasing the strength. Water is used to mix the microfine cement and admixtures to form a grout. The water quality should be potable and free of impurities that can affect the grout performance. Equipment such as mixers, pumps, hoses and packers are used to prepare, transport and inject the grout into the rock or soil mass.
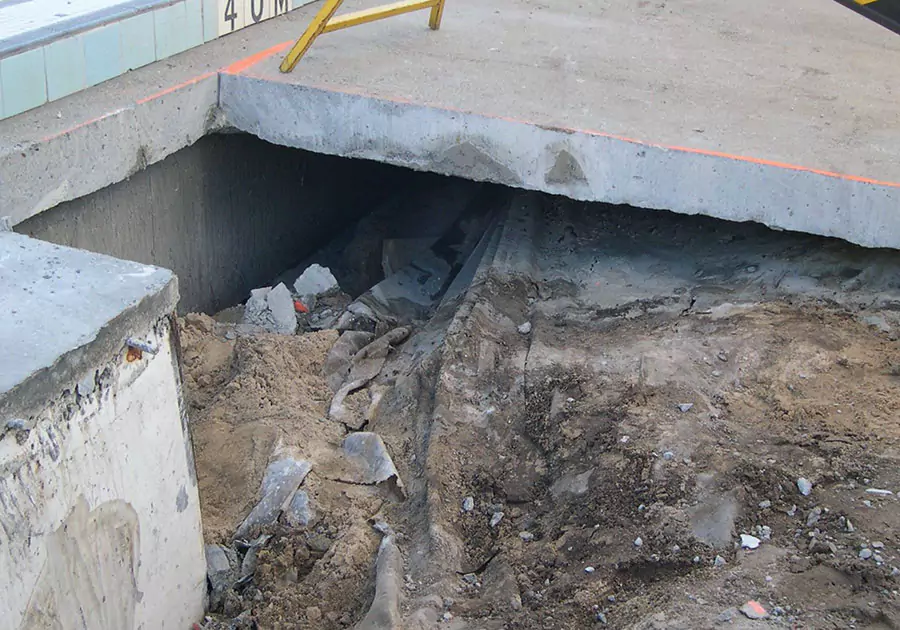
Grouting methods
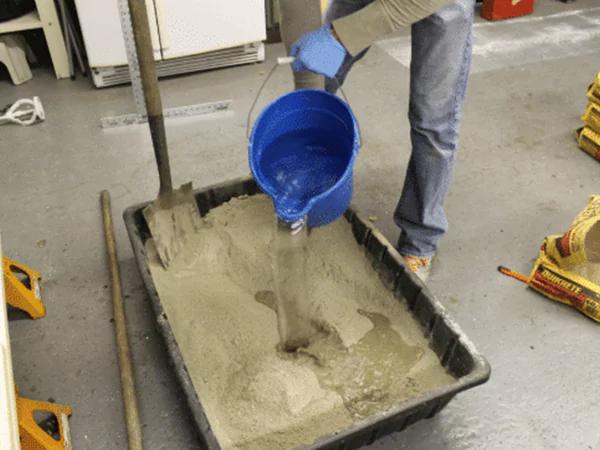
1st step
The water-cement ratio is determined based on the desired grout consistency, viscosity and strength. The water-cement ratio should be as low as possible to achieve a high strength and low permeability grout.
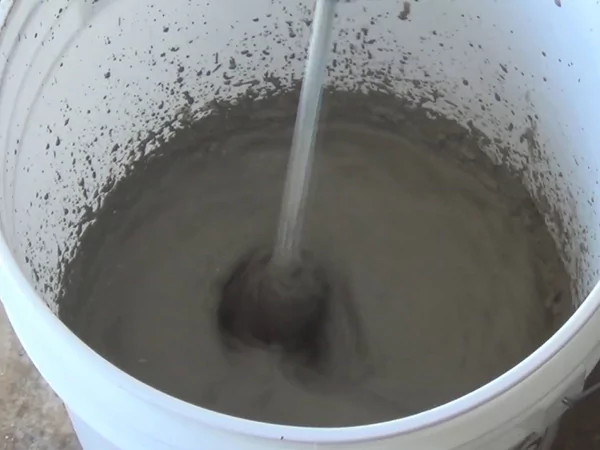
2nd step
The microfine cement and admixtures are mixed with water in a high-speed mixer for a sufficient time to ensure a homogeneous grout without lumps or segregation.
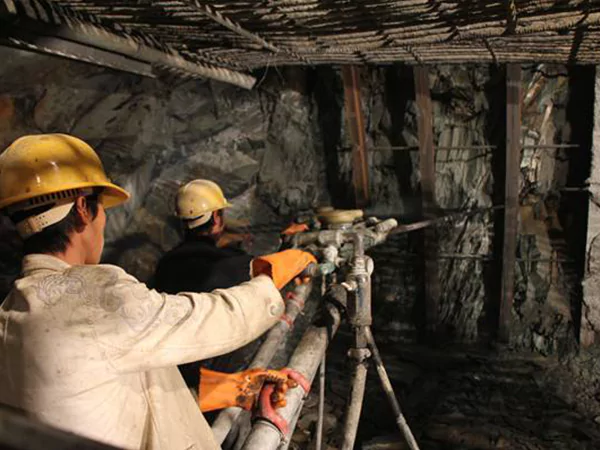
3rd step
The grout is transferred to a pump that can deliver a constant pressure and flow rate to inject the grout into the rock or soil mass.
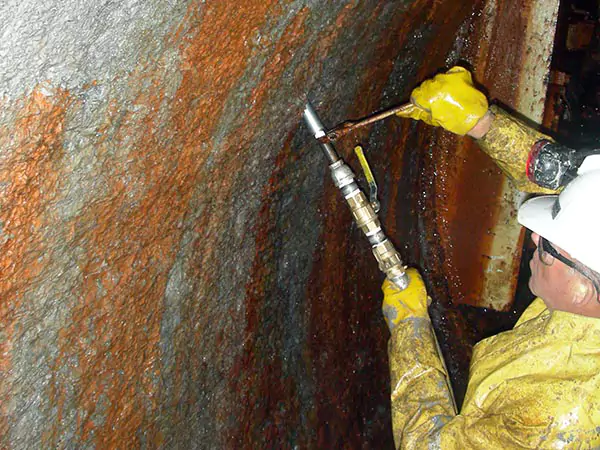
4th step
The injection points are selected and prepared using packers or other devices that can seal the boreholes or cracks from where the grout is injected
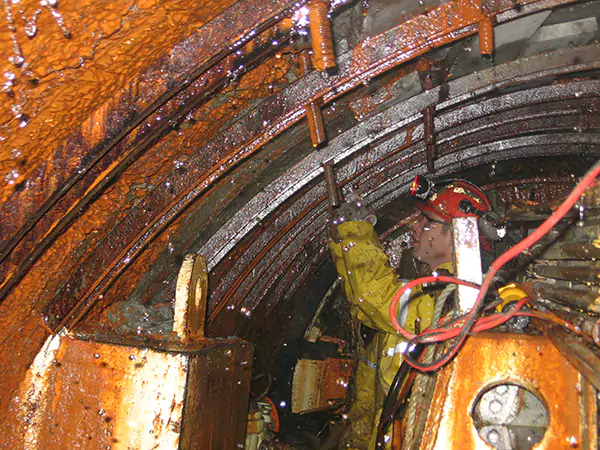
5th step
The grout is injected into the rock or soil mass following a predetermined sequence and pattern that can ensure a uniform distribution and penetration of the grout
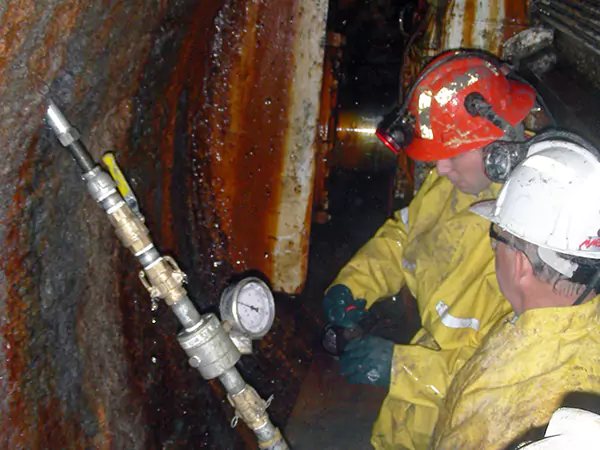
6th step
The injection pressure and volume are monitored and adjusted according to the site feedback and grout behavior